
What Does "Validation-Ready" Mean?
IMPAK offers several sealers that are designated as validation-ready. Heat sealer process validation is a critical aspect of ensuring that heat sealing equipment performs consistently and reliably, especially in medical device and pharmaceutical packaging applications. The goal of process validation is to verify that the heat sealer can produce seals of the desired quality under consistent and controlled conditions, and thereby maintain a standard for packaging sterility.
Although validation protocols differ between companies and applications, FDA regulations generally require sealers used for sterile medical pouch sealing to be ISO 11607-compliant. This refers to internationally-recognized standards regarding various aspects of sterile packaging. In order to be ISO 11607-compliant, a heat sealer must be subject to rigorous validation protocols; a sealer that is built to accomodate the expected steps in this process is considered "validation-ready."
val • i •'dat • a • tion
(adjective) The act of making something legally or officially acceptable or approved, especially after examination
from the Latin root "validus," meaning strong, powerful, healthy, or, having legal force
Seal process validation itself typically involves conducting a series of tests to verify that the heat sealer works as intended. This three-phase process includes:
- Installation Qualification (IQ): Verifying that the equipment is installed correctly and meets specified requirements.
- Operational Qualification (OQ): Testing the system under normal operating conditions to ensure that it produces consistent results within the defined parameters.
- Performance Qualification (PQ): Running the system for a longer period and in real-world conditions to demonstrate that the process will consistently produce high-quality seals over time.
As part of the validation process, critical process parameters (CPPs) are defined. These are the factors that directly impact the quality of the seal. Common CPPs for heat sealing include:
- Temperature: The sealing temperature is critical to achieving the proper bonding of materials.
- Pressure: The amount of pressure applied during the sealing process to ensure proper fusion of the materials.
- Time: The duration of the sealing process needs to be optimized for adequate bonding without over or under-processing.
Is Validation the Same as Calibration?
Though the terms are related, calibration is not the same as validation in this context. As outlined above, validation is a highly regulated and documented holistic process intended to ensure that a heat sealer conforms to established standards from the time it arrives and is installed in the facility where it will be operated through every aspect of its use, including operator training, preventative maintenance, and malfuntion resolution protocols.
Calibration, on the other hand, is specifically the act of testing sealer performance (seal time, temperature, and pressure) and making any needed adjustments to ensure optimal accuracy. This is normally performed by a licensed technician, and it is customary for this technician to be from a third party rather than the manufacturer.
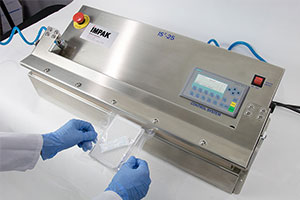
IMPAK's iS2-25 Validation-Ready Sealer
IMPAK Corporation is proud to partner with many companies involved in pharmaceutical and medical device packaging. We understand the intricacies of the sealer validation process and strive to make that process as seamless as possible for our customers. Each of the sealers in our MPDSS Series and iS2 Series is equipped with a port designed for easy interface for validation and calibration processes. The state-of-the-art controllers on these sealers allow for superior precision when setting seal time, temperature, and pressure. The iS2 platform, built with Siemens PLC and HMI, is highly sophisticated and versatile, and IMPAK has been engaged to retrofit many older sealers with this popular control system.
IMPAK has also configured other sealers to fit specific validation protocols. Our engineers have designed and manufactured, for example, validation-ready vacuum sealers, with an option available to allow validation of vacuum integrity in addition to seal time, temperature, and pressure. Contact us to find out more about our validation-ready capabilities for vcacuum sealers or any other type of sealing machine.