
Explosion-Proof Sealers
Certified Explosion-Proof Heat Sealing Machines
For Hazardous Locations
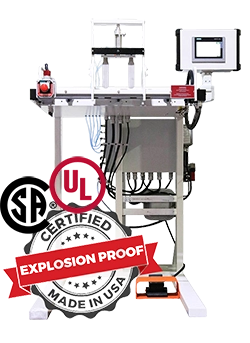
Many companies have production facilities that, due to the nature of the materials used therein, are classified as hazardous locations for the operation of electrical or electronic equipment. Sparks, arcs, and heat produced by electrical machinery in an environment in which flammable gasses, combustible dust, or ignitable fibers are present can and will cause fires or explosions if equipment is not properly configured for safe operation. As a manufacturer of highly sophisticated heat and vacuum sealing machinery, IMPAK is well acquainted with these risks, and has worked with many companies to produce explosion-proof sealers that conform to the most rigorous standards.
IMPAK has nearly 10 years of experience working with Nationally Recognized Testing Laboratories (NRTLs) to build tested and trusted explosion-proof sealing equipment. Each unit is made to order for the specific location in which it will be operated, undergoing thorough testing during the process to confirm compliance, and is sent to a third-party facility for accredited certification. Sealers can be built with or without vacuum functionality, in horizontal or vertical orientation, and with seal lengths of 110" and beyond. Each explosion-proof unit comes with our state-of-the-art Intelligent Sealing System (iS²) and Temperature Controller (+/- 3deg) for accurate and reliable results every time.
Available Options
Horizontal or Vertical Orientation
Vacuum Seal System
Cleanroom Ready Design
3rd Party Calibration Services
Validation System
SS or Powder Coated Body
"Enclosed in a case that is capable of withstanding an explosion of a specified gas or vapor that may occur within it and of preventing the ignition of a specified gas or vapor surrounding the enclosure by sparks, flashes, or explosion of the gas or vapor within, and which operates at such an external temperature that a surrounding flammable atmosphere will not be ignited thereby.”
– Article 100 of the NEC describing an Explosion-Proof Apparatus
Hazardous locations are designated in the United States by the NFPA 70 National Electric Code, which provides a class, division, and group system to categorize not only types of hazardous materials, but also operational conditions. NFPA 70 NEC also uses a version of the Zone System based on the IECEx system instituted by the International Electrochemical Commission (IEC) which reflects requirements set out by Europe's ATEX directives and is more commonly used outside of the U.S. and Canada (see below). The Occupational Safety and Health Administration (OSHA) references these classifications and requires that equipment used in hazardous locations is clearly designated with the appropriate class, group, and operating temperature for which it is approved.
From Class I, Division 1 to Class III, Division 2 and all related groups therein, IMPAK makes sealers for ALL hazardous locations.
NFPA 70 NEC Hazardous Location Classification
Class | Division | Group |
---|---|---|
I – Flammable gases or vapors may be present | 1 – Flammable concentrations exist under normal operation conditions 2 – Flammable concentrations exist under abnormal operation conditions |
A – acetylene |
B – hydrogen, butadiene, ethylene oxide, propylene oxide, and acrolein | ||
C – ethylene, cyclopropane, and ethyl ether | ||
D – acetone, ammonia, benzene, butane, ethanol, gasoline, hexane, methane, methanol, methane, naphtha, natural gas, propane, and toluene | ||
II – Combustible dust may be present | 1 – Combustible concentrations exist under normal operation conditions 2 – Combustible concentrations exist under abnormal operation conditions |
E – combustible metal dusts: aluminum, commercial alloys, and magnesium |
F – combustible carbonaceous dusts: carbon black, charcoal, coal, and coke dusts | ||
G – other combustible dusts: chemicals, flour, grain, plastic, and wood | ||
III – Easily ignitable fibers or flyings may be present | 1 – Ignitable concentrations of hazards exist under normal operation conditions 2 – Ignitable concentrations exist under abnormal operation conditions |
n/a |
Examples of Hazardous Locations
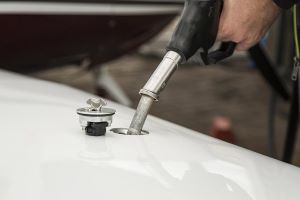
Class I - Flammable Gas
Class I locations are catagorized by a presence of flammable gasses or vapors in the vicinity such as natural gas, gasoline vapors, or other chemical accelerants. In these conditions, the potential for a spark to cause ignition cannot be ingored.
- Oil refineries
- Aircraft hangars
- Fuel servicing areas
- Chemical plants
- Dry cleaning plants
- Spray painting facilities
- Commercial garages
- Bulk storage plants
- Areas with liquefied petroleum
- Areas with natural gas
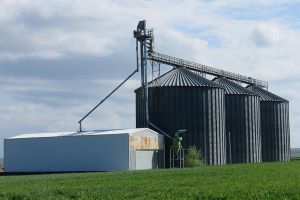
Class II - Combustible Dust
Class II hazardous locations have a presence of combustible materials suspended in the air. Dust and particles can cause powerful explosions after being exposed to a spark in certain conditions.
- Grain elevators
- Flour and feed mills
- Plants with magnesium or aluminum powder
- Medicine manufacturing plants
- Producers of starch or candies
- Sugar and cocoa processing plants
- Locations with fireworks
- Coal plants and other carbon handling areas
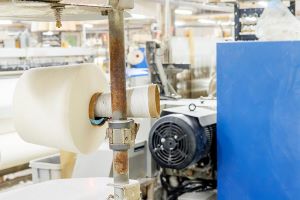
Class III - Ignitable Fibers
Class III locations have areas with easily ignited fibers close enough to equipment to make a spark a fire hazard.
- Paper mills
- Textile mills
- Clothing manufacturing
- Plants with cut wood and/or heavy sawdust
- Paper recycling facilities
IEC Hazardous Zone Classification
Ignitable concentrations of flammable gases or vapors are... | 0 - present continuously or for long periods of time |
1 - likely to occur under normal operating conditions or may exist frequently because of repair, maintenance operations, or leakage | |
2 - not likely to occur under normal operating conditions and if they do will only persist for a short period of time; may become hazardous only in case of an accident or some unusual operating condition | |
Combustible dusts or ignitable fibers/flyings are... | 20 - present continuously or for long periods of time |
21 - likely to occur under normal operating conditions or may exist frequently because of repair, maintenance operations, or leakage | |
22 - not likely to occur under normal operating conditions and if they do will only persist for a short period of time; may become hazardous only in case of an accident or some unusual operating condition |
Below, one of IMPAK's explosion-proof sealers undergoes third-party calibration.
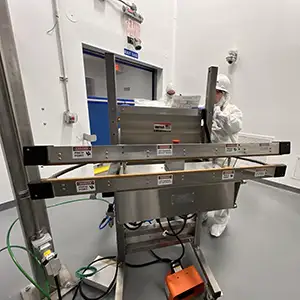
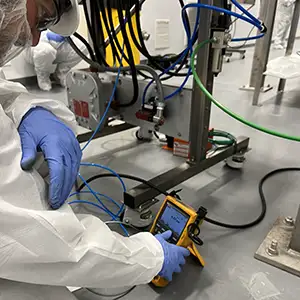
"IMPAK worked backwards from our certification specifications to produce equipment specifically made to meet our exact needs.”
– Engineering Manager, Major Chemical Producer for U.S. DOD
Certified Explosion Proof vs. “Built-in-Accordance”
For projects where the environment requires strict safety standards, IMPAK brings decades of experience in the packaging industry to ensure your equipment maintains safety and efficiency standards. This is especially important for those working with US or Foreign military organizations - your machine needs to stay in spec consistently. If your project requires full UL / CSA certifications prior to installation, we can work with you to coordinate with the certifying agency ahead of shipment.
For customers who do not need a cerification on file, we offer our "Built In Accordance" option. We use our exerience and most current understanding of certification requirements to build the machine to meet those high standards. For some customers, this can save both time and the high certification fees. Please note that this option is not certified by any agency, and you take on the risks involved. To this end, the unit would no longer be labeled as "Explosion-Proof" without final certifications.

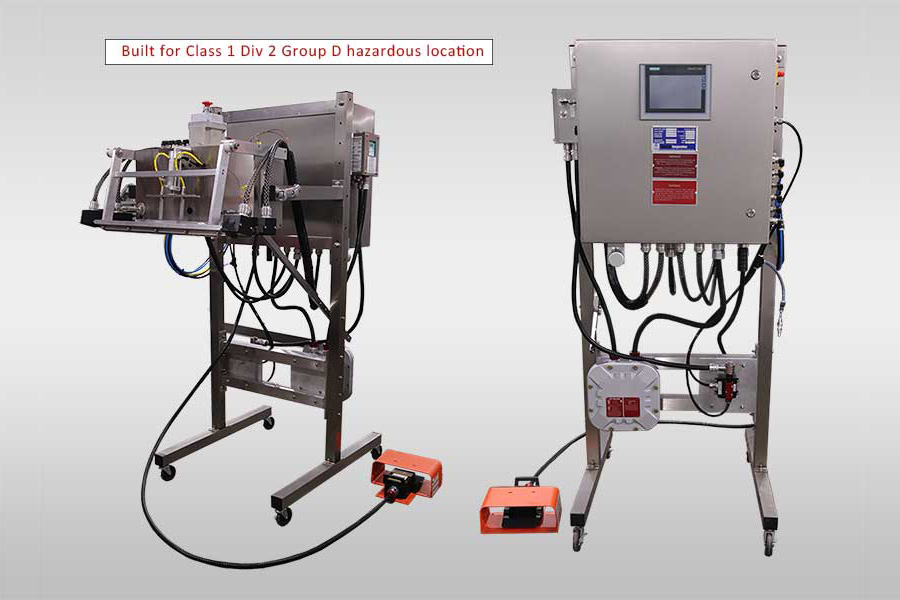
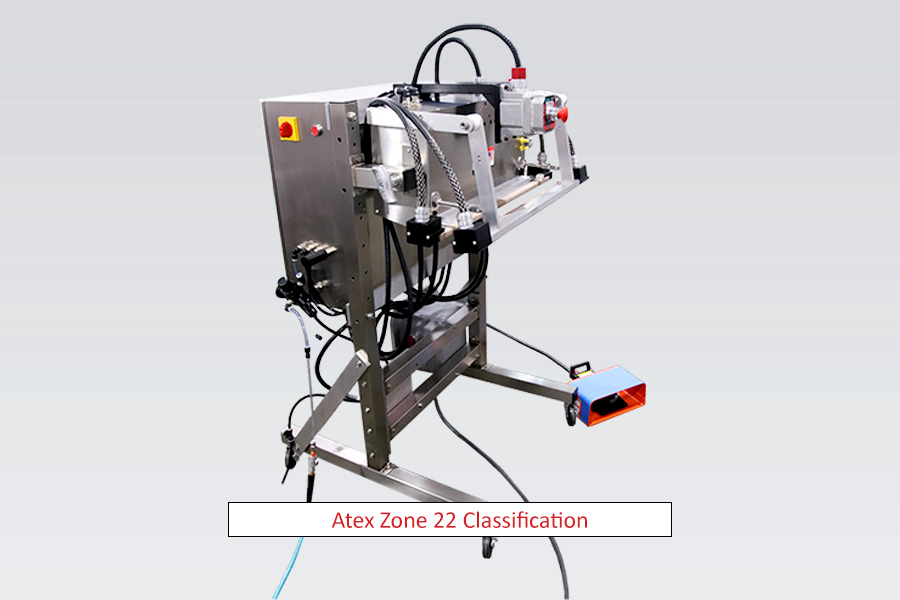
“I went with IMPAK because they were the only company that insisted on third-party certification with all the documentation I required. ‘Explosion-proof’ isn’t something I can simply take a company’s word on.”
– Project Manager, U.S. Military Munitions Ordnance Group
Explosion Proof Sealer Videos
Built in Accordance with: Class 1 | Div 1 | Group A
Built in Accordance with: Class 1 | Div 2 | Group D
Vertical Vacuum Unit for Military Application
Horizontal Vacuum Unit for Aerospace Application
Custom Configurations
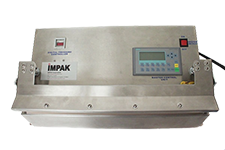
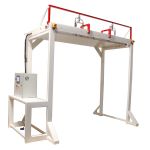
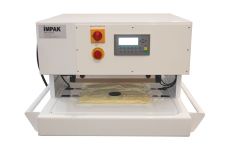
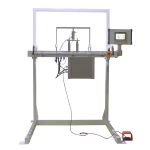
We mention going up to 110" seal lengths and beyond, but the truth is we make the right machine for your needs. We can provide the same reliability and safety even with smaller sizes suitable for tabletop use.